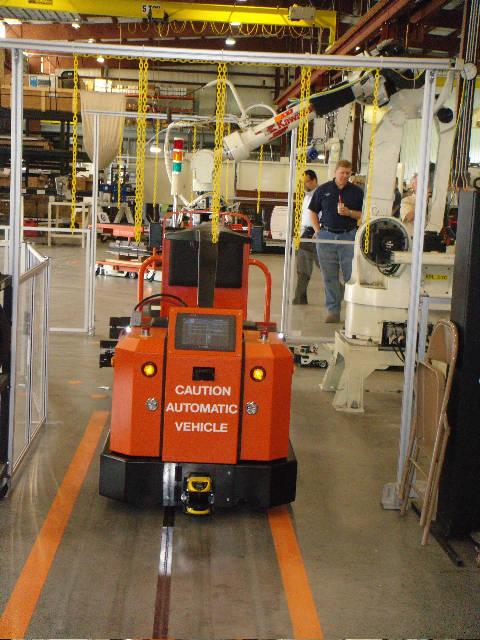
Assembly line warehouses have slowly developed into one of the most efficient ways to pick, pack, assemble and disassemble products from inventories as needed. The earliest examples and the basic concepts behind the process relied largely on manpower to move merchandise and handle materials. Automation helped to reduce the strain on individuals and made the line move much faster. Modern wireless technology, advances in computing and a better overall infrastructure have resulted in technologies and practices that have helped to create massive centers that operate incredibly efficiently despite handling thousands of individual pieces of inventory.
Advanced automation of basic processes has made some of the largest leaps in recent years. Moving materials from inventory to an assembly line was done by laborers at first and by drivers using forklifts and other machines later. In large warehouses fulfillment can come to a halt if materials are not moved efficiently. The newest technology for performing this task is known as an automatic guided vehicle (AGV). These are computer controlled carts that can navigate a warehouse without any human intervention. An AGV can be combined with an automated inventory retrieval system so that loads of a single material or product can be picked from shelves and then delivered to an assembly line for use by workers with just the click of a button.
West Coast Distribution warehouse technology has advanced to the point where it is possible to build a modular assembly line. These are sequences of rolling panels that can be moved, modified and resized as needed. The destination of the assembly line can be changed or the origin of materials upstream can be switched. A company can also change an entire warehouse assembly line setup in just a few hours to accommodate larger parts or different picking and packing techniques. This technology can also be applied to inventory shelving and storage. Shelving units can be moved so they are lower to the ground when in use and then lifted up above other shelving units during periods when the area will not need to be accessed.
Most assembly line warehouses have progressed dramatically when it comes to worker safety. Employees on some assembly lines have workstations that have been catered to their personal needs. Understanding of ergonomics and stress have made it possible to fine tune an assembly line so that repetitive injuries are reduced and employees can work for longer periods of time without becoming fatigued. Complimentary technologies like radio-frequency identification (RFID) help employees to perform tasks like scanning and physical inventories without having to strain muscles or over-exert in order to reach specific products.